EQL
The Express Quantometric Laboratory is established for rapid on-the-spot quantitative analysis of steel test pieces incoming from the steel production shop for the purpose of timely corrections of the chemical composition of the liquid metal. The metal samples are sent within 30 seconds directly to the laboratory by compressed air pipe.
The principal laboratory equipment and instrumentation comprise:
- Stationery emission quantometer Type: Spektromax Producer: "Spectro Analytical Instruments" GmbH & Co. KG ("Ametek Group", USA)
- Mobile analyser Type: Spektrotest Producer: "Spectro Analytical Instruments" GmbH & Co. KG ("Ametek Group", USA)
- Automatic analyser Type: Leco CS - 244 Producer: LECO Instruments GmbH, USA
- Automatic analyser Type: Leco RH - 1E Producer: LECO Instruments GmbH, USA
- Automatic analyser Type: Leco TC - 136 Producer: LECO Instruments GmbH, USA
- Electronic scanning microscope Type: S 405 A Producer: HITACHI, Japan
- Electronic scanning microscope Type: S 550 Producer: HITACHI, Japan
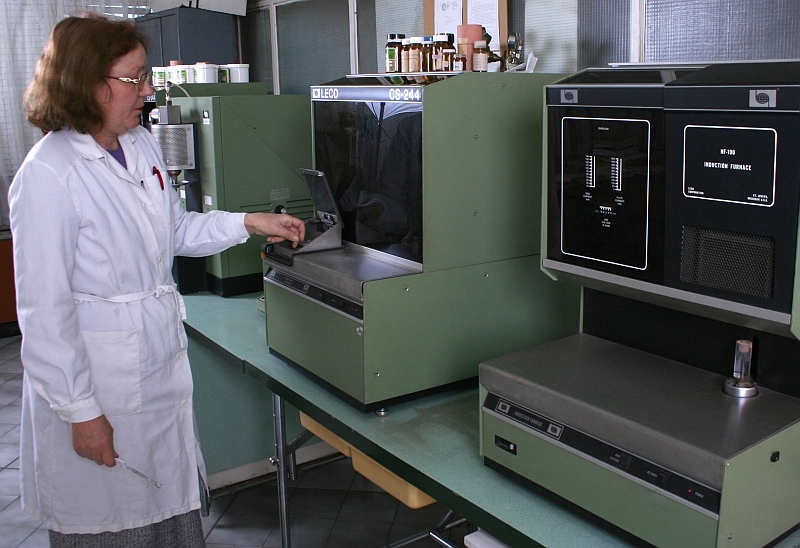
Non-Destructive Test Laboratory
Established in 1986 the Non-Destructive Testing Laboratory has a highly skilled and well trained as per EN 473 personnel performs the necessary ultrasonic, magnetic-particle, dye-penetrant, eddy-current and visual tests. The specified methods are used for controlling of internal and surface condition of large-scale castings and forgings as well as welded joints. Assessment of the strict design conformity is made as per existing international standards.
For the different experiments the laboratory is equipped with modern non-destructive test instruments produced by "KRAUTKRAMER" and "KARL DEUTSCH".
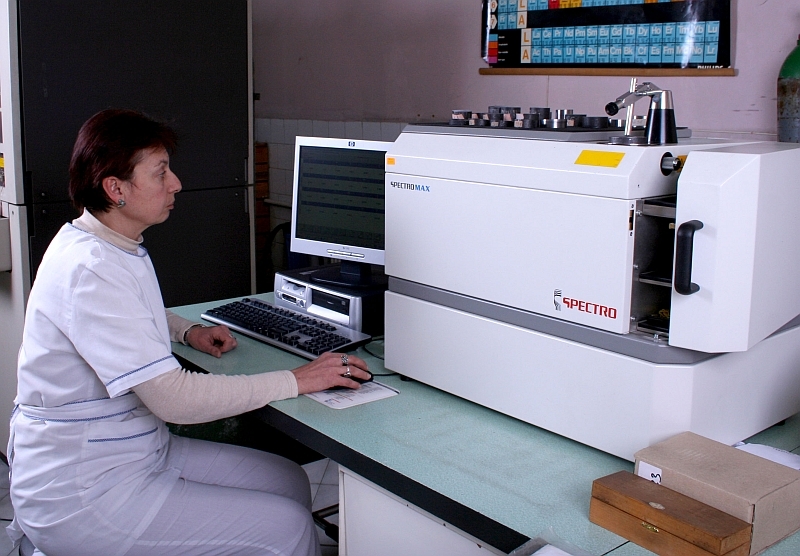
Maching Shops
The shops are equipped with numerous machines for both rough and final machining of forgings and castings, namely lathes (vertical and for turning of rotating details), boring machines, drilling machines, milling cutters and grinders, mostly CNC equipped, which enables the production of rough and finish machined details.
Lathes
Dimensions of machined details:
For rough machining:
Length: 14 000 mm
Diameter: 2 500 mm
Maximum weight: 120 ton
For final machining:
Length: 10 000 mm
Diameter: 1 800 mm
Boring machines
Maximum dimensions of machined details:
Diameter: 3 500 mm
Height: до 3 500 mm
Width: до 1 900 mm
Length: 8 000 mm
Spindle (250 mm / 1900 mm run) can be combined with rotary table, designed for details of up to 8 tons.
Vertical lathes
Maximum dimensions of machined details:
Diameter: 3 800 mm
Height: 2000 / 3000 mm
Weight: up to 25 tons
Hollow Bore Drilling machines
two-sided drilling of details up to 20 000 mm
one-sided drilling of details up to 10 000 mm
Maximum diameter of machined details: up to 1 000 mm
Weight: up to 20 tons
Drilling of hollow bores of 40 to 200 mm has been adopted, with maximum length depending on the technical parameters of the particular single details.
Milling cutters
3-coordinate milling cutter (type "machining center") allows machining of details with the following parameters:
Maximum dimensions: 800 W x 1 000 L x 800 H
Weight: up to 450 kg
Honing machine
Maximum dimensions of machined details:
Diameter: 250 mm
Bore diameter: 120 mm
Length: 5 000 mm
Alignment Grinders
Maximum dimensions of finish machined details:
Diameter: 1000 / 1 600 mm
Length: 5000 / 6 000 mm
Weight: up to 14 / 50 tons
The hardware machining park consisting of vertical lathes and boring machines enables final machining of instrumental steel products with the following parameters:
Diameter: 20 000 mm
Height: 16 000 mm
Weight: up to 120 tons
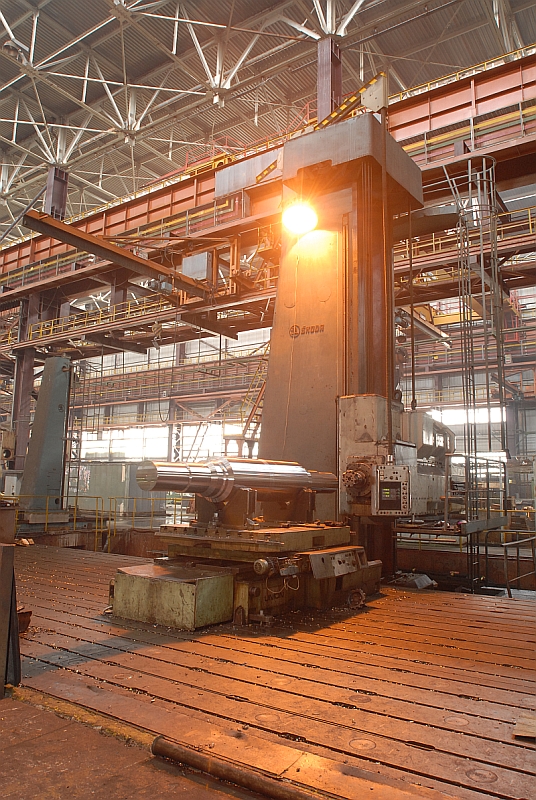
Forging and Heat Treatment Shop
tructurally the Forging and Heat Treatment Shop comprises:
> Forging Press Section with annual forging capacity of 45 000 tons.
Principal equipment includes:
3 600 / 4 500-ton Forging Press.
Type: vertical 4-column, oil-hydraulic
Operating pressure: max. 250 kg/cm2
Dimensions: Vertical clearance - 5 000 mm
Column distance: 4 200 x 2 300 mm
Table: 2 500 x 6 000 mm
Producer: Kobe Steel - Japan Rotation and linear-progressive motion of the forging are implemented through 160-ton Forging Manipulator.
1 600-ton Open-die Forging Press
Type: vertical 2-column, oil-hydraulic
Operating pressure: max. 250 kg/cm2
Dimensions: Vertical clearance - 3 000 mm
Column distance: 2 600 x 1 700 mm Table: 1 600 x 3 000 mm
Producer: Kobe Steel - Japan Forging motions are implemented through 40-ton Forging Manipulator.
Heating Furnaces
150-ton 1
100-ton 5
50-ton 2
Annealing Furnaces
150-ton 1 Inner dimensions: 4 000 W x 10 000 L x 3 500 H
150-ton 1 Inner dimensions: 3 000 W x 14 000 L x 3 000 H
90-ton 4 Inner dimensions: 3 000 W x 10 000 L x 2 500 H
35-ton 1 Inner dimensions: 2 500 W x 6 000 L x 2 500 H
Producer: Sankin Sangiyo - Japan
> Heat treatment section with heat treatment capacity of 3 400 tons of rolls for cold rolling and 23 000 tons of large-scale rotary and frame details. The technological equipment in this section allows implementation of all types of heat treatment of rotary parts - mainly rolls for cold rolling, back up rolls, etc.
The principal heat treatment equipment includes:
Horizontal Heat treatment Furnaces
100-ton 1 Inner dimensions:2 500 W x 14 000 L x 2 300 H
100-ton 1 Inner dimensions:4 000 W x 8 000 L x 2 800 H
90-ton 5 Inner dimensions:2 500 W x 9 000 L x 1 800 H
25-ton 3 Inner dimensions:1 000 W x 7 500 L x 1 000 H
15-ton 2 Inner dimensions: 1 200 W x 5 000 L x 1 300 H
30-ton Horizontal Resistance Furnace
Inner dimensions: 1 000 W x 5 000 L x 1 800 H
Differential Rapid Heating Furnace, designed for differential quenching of back up rolls for hot and cold rolling with capacity up to 30 tons.
Components size:
Dia: 600 - 1 450 mm
Length: до 3 000 mm
Dual Frequency Induction Hardening Installation for forgings with weight up to 13 tons.
Components size:
Rolls' dimensions:
Barrel diameter: 200 - 900 mm
Total length: 7 000 mm
Producer: Kobe Steel - Japan
Subzero Treatment Chamber
Inner dimensions: 900 W x 7 000 L x 1 000 H
Capacity: 13 ton
Coolant: liquid nitrogen
Operating temperature: minus 195,8 0C
Producer: Kobe Steel - Japan
Surface Layer Quenching Machine (mist, water, air type)
Capacity: 90 ton
Maximum length of processed forging: 6 000 mm
Maximum barrel diameter: 3 000 mm
Surface Layer Quenching Machine (mist, water, air type)
Capacity: 13 ton
Maximum length of processed forging: 6 000 mm
Maximum barrel diameter: 3 000 mm
Oil Tempering Tanks, intended for tempering up to 150 C
10-ton Vertical Heat Treatment Furnace
50-ton Vertical Heat Treatment Furnace
Tough Quenching Oil Tanks
Tough Quenching Water Tanks
All installations are equipped electronically and computerized for monitoring, control and recording of forging and heat treatment processes.
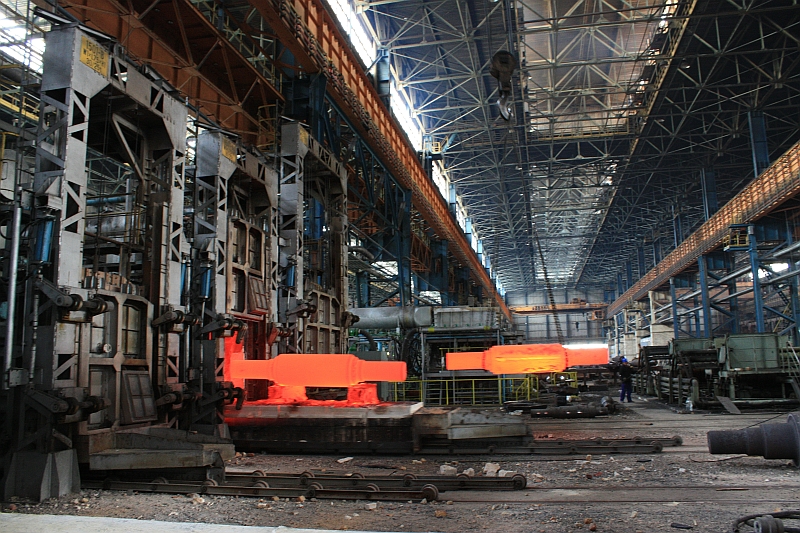
Pattern shop
The Pattern shop is designed for processing of 6 000 m3 timber annually. It is intended for manufacturing of complex wooden patterns, timber drying processes, timber fumigation and preparation of wooden crating. Maximum diameter of working patterns can reach up to 8 000 mm.
The principal shop equipment comprises:
Wood processing machines for preparation of wooden patterns - lathes, presses, milling and grinding machines.
Timber Drying Chambers with length up to 8 000 mm.
Spray Painting chambers for wooden patterns.
Timber storage with total area of 50 000 m2 .
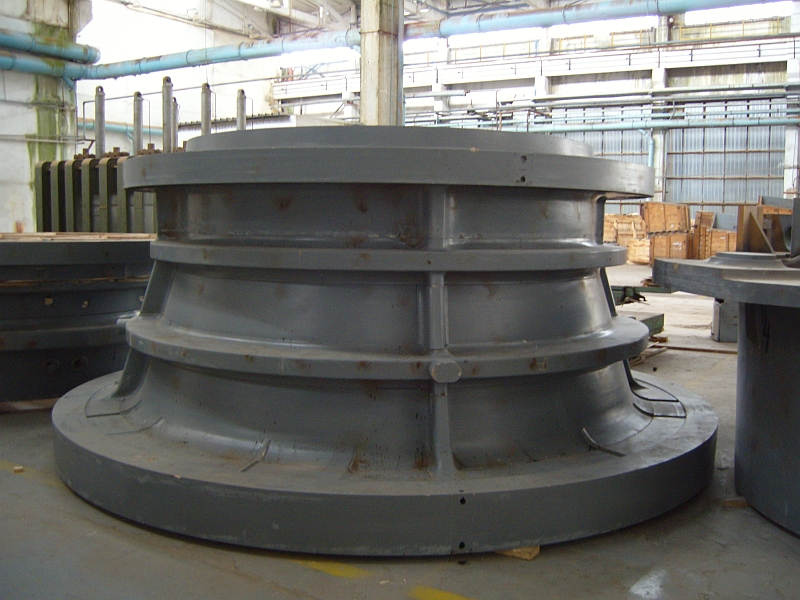
Fettling Shop
The Fettling shop is designed for finishing of the castings. Final treatment of castings covers removal of the gating system and the risers and repair of the casting defects. Final cleaning of the castings in Shot Blasting chamber and heat treatment for stress relief are accomplished there.
Precise dimension laying-out of the castings prior to machining is carried out. Non-destructive control, including Ultrasonic examination, Magnetic particle test, and Dye penetration examination is being carried out after rough (initial or intermediate) machining by means of modern equipment.
The principal equipment embraces:
4 Shot Blasting chambers of 30-tons, 60-tons and 150-tons capacity with maximum dimensions of 9 000 W x 9 000 L x 7 000 H.
11 Heat Treatment Furnaces of 50-tons, 80-tons, 150-tons and 250-tons capacity with maximum dimensions of 9 000 W x 13 000 L x 4 000 H. The computerised combustion control ensures achieving of high temperature homogenity within the furnace space, thus guaranteeing precise implementation of thermal conditions.
Different tools for exterior cleaning and removal of uneven particles from the non-machineable casting surfaces.
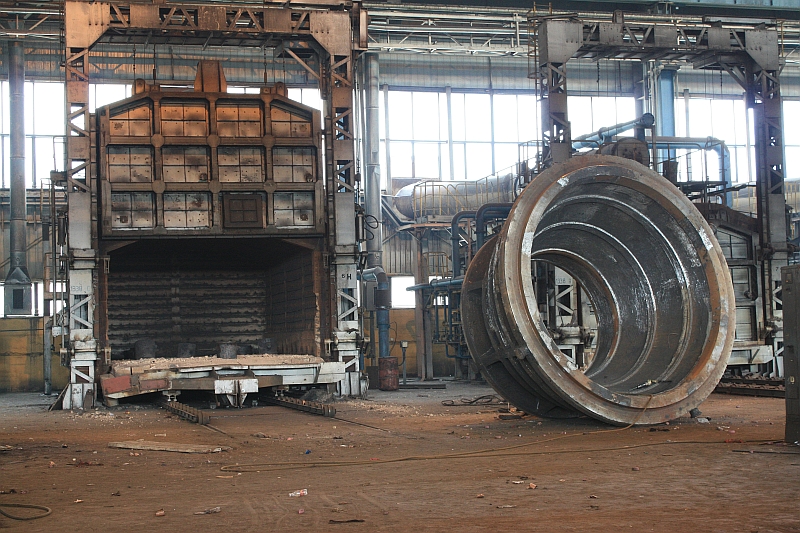
Steel Foundry
The Steel Foundry is designed for annual production of 25 000 tons of castings with unit weight from 4 to 120 tons. The moulding mixtures, used in the moulding process, are self-hardening on the basis of quartz sand, water glass and catalyst, or quartz sand, furan resin and catalyst. Casting moulds are implemented by means of chromite sand at the contact points between liquid steel and casting mould, as well as at the thermal spots, in order to reduce the mechanical and chemical blind scab. The regulation of heat balances is achieved through the use of exothermic and insulating materials.
The principal technological equipment comprises:
Automatic Moulding Line for castings of 3 to 5 tons weight with annual production of 11 000 tons.
Casting pits for castings of 20 to 50 tons and 50 to 120 tons weight with annual production of 14 000 tons.
Core-making equipment, designed for manufacturing of cores with volume of up to 1000 dm3.
Knock-out grids, used for rough cleaning of the castings from moulding sand residues.
Mixers for mechanical preparation of moulding sand mixtures.
Mobile and stationary feeders, intended for mechanical feed of moulding sand.
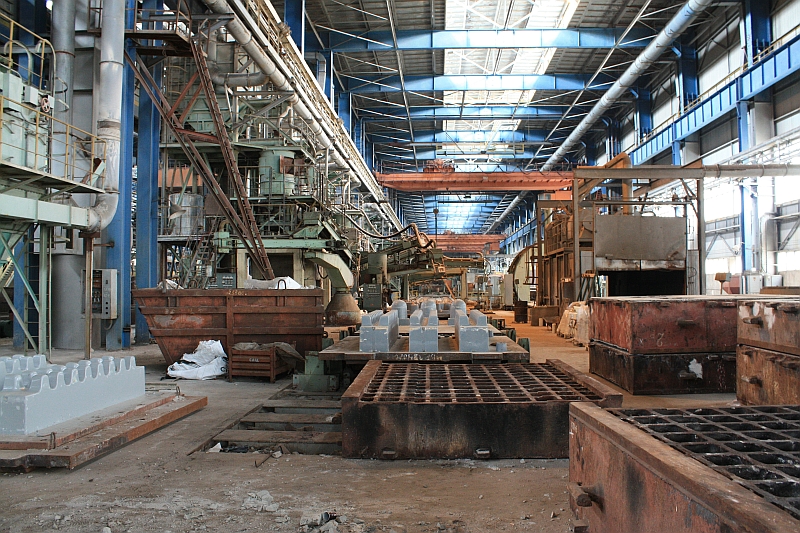
Steel Production Shop
The Steel Production Shop is designed for the production of 150 000 tons of liquid steel per year. The main technological equipment covers:
Three electric arc furnaces of 15-tons, 25-tons and 60-tons capacity (designed and manufactured by "BBC", Switzerland) for production of liquid steel from scrap by means of powerful electric arc. The furnaces are equipped with voltage transformers of 20 000 volts, while electric arc is being ignited by means of carbon electrodes.
Vacuum installation for post furnace vacuum treatment of steel (made by "Standard Messo", Germany) used for treatment of liquid steel under high vacuum. Structurally the installation comprises:
VAD installation of 12 to 70-tons capacity, designed for production of forging ingots.
VOD installation of 25 to 70-tons capacity, designed for production of high alloyed and stainless steel.
Teeming ladles of 15-tons, 25-tons and 60-tons capacity, used for transportation of liquid metal from electric arc furnaces to its pouring location.
75 000 tons of forging ingots with unit weight of up to 80 tons can be produced at the shop per year. An Electro Slag Remelting Installation, designed for production of ingots up to 25 tons, is being assembled and put into operation, with a start up date end of December 2008.
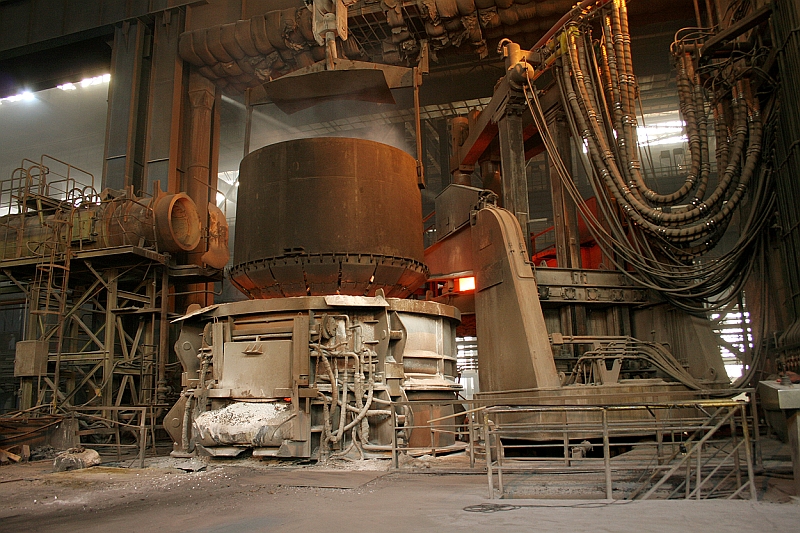
Scrap Yard
The Scrap yard's purpose is the preparation of charge through sorting the scrap by size and type of steel, crushing it to smaller pieces, filling of the scrap bucket and its transportation to the Steel production shop.
The shop equipment includes:
Briquetting press (made by "Arnold", Austria), designed for chips sealing.
Shears (made by "Tesuka", Japan), designed for scrap and sheet metal cutting.
Gas-cutting machines, designed for gas-cutting of solid metal details up to 2200 mm thick.
Weighing machines with capacity of 15, 25 and 60 tons capacity, for weighing of scrap prior to its transportation to the Steel production shop.
Haulage trucks of (load capacity 30 tons), running on rails, connecting the plant's sections.
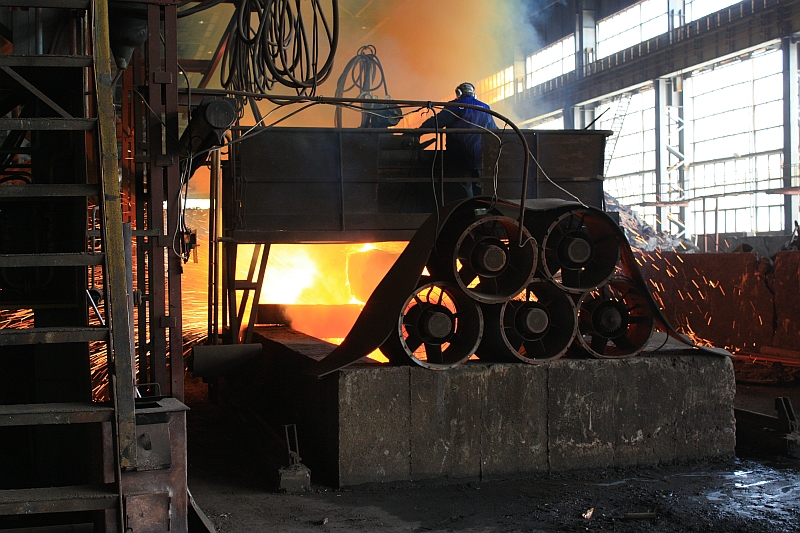